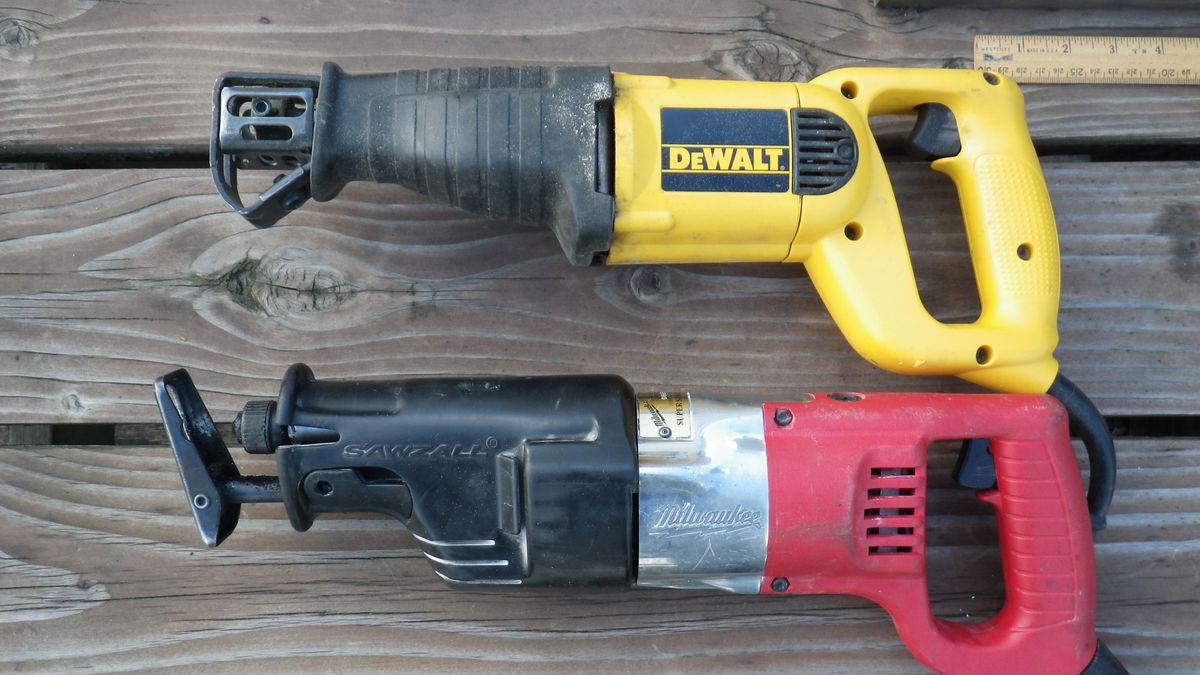
The Reciprocating Saw: A “Fresh Look” at a Familiar Tool
February 9th, 2014
Categories
by Paul Bindon and Matt Stroud
Over the years we have attended and instructed at many auto extrication events around the country. When using the reciprocating saw, we have noticed varying skill levels being demonstrated by students and instructors alike. Most of the time, the saw is used at full speed, while the operator tries to hold on, as the tool throws them back and forth at 3000 strokes per minute (SPM), until there is smoke and sparks and the blade goes dull since the teeth melted off. A quick blade change is performed, and you are back to cutting, until the blade goes dull again, then repeat… Often there can be a large pile of dull blades by the end of the training evolution. Many more are used by the end of the weekend. Almost all of them are missing a one inch section of teeth. We have witnessed the common trend that is referred to as, wide-open-throttle-itis! It seems that when we (yes, we’re guilty too) get any power tool in our hands, our natural reaction is to pull the throttle until the tool has reached maximum RPM before we use it. This “wide open” or “full throttle” power tool use has been engrained in you since you first picked up a chain saw in the fire academy. If you train with your saw at high speed, you tend to use it at high speed in the field. When responding to an MVA where extrication is necessary, injured patients require our best use of time. It is a natural instinct to believe faster is always better. Since gas engines require rotational momentum to reach the peak of their power band, it makes perfect sense to run a chainsaw or rotary saw at full throttle to keep it from stalling or binding during a cut. Electric power tools, such as a reciprocating saw, can supply the needed torque for cutting at almost any RPM.
It seems that there has been little thought put into the proper application of the saw, the design of the blade, and the types of metal being cut during auto extrication. A reciprocating saw is a very valuable and inexpensive tool being used around the world for many applications. What is the best way to utilize them?
We have taken it upon ourselves to go outside the box, back to the beginning to teach ourselves how the tool operates in today’s environment with the challenges of cutting different metals. After decades of personally using these tools, the results of our extensive testing really surprised us. In this article, we will be exploring metallurgy, tool use, blade types and design, and application, along with some little tricks we learned along the way.
Brief history of the tool commonly known as a “Recip Saw”
Milwaukee Electric Tool Corp. was the first to market a reciprocating saw named the “Sawzall” in 1951. The reciprocating saw has a cutting action that pushes and pulls the saw blade back and forth with a counterweight that helps stabilize it. This saw design has evolved with the introduction of features such as variable speed, adjustable shoe, quick change blades, and battery power for the electric motor. Battery power for the saw enables the operator to work just about anywhere without the need for a 120V power supply.
The anatomy of the saw and how it works
The shoe provides a bracing point for the saw and helps keep it from jumping around too much. The shoes can be fixed or adjustable. The adjustable shoe allows the operator to adjust how deep the blade penetrates into the material being cut.
As seen above, a quick change blade mechanism makes blade changes possible without tools or long delays in operation. This makes it easy to change blades when they overheat and dull due to high speed operation. What if you don’t have 15 blades in your pocket that may be needed to complete the cut you are doing at maximum blade speed?
Orbiting or straight cut actions
Some saw models have the added option of an orbital action. This action allows the blade to trace an oval pattern, lifting the teeth over the material and drawing them back during the cutting stroke for faster cutting of materials. In our testing we found no benefit in using this more expensive version of the saw.
Variable speed option
The variable speed feature enables the operator to change blade speed from 0 to 4000 SPM, with an average maximum speed of 3000 SPM. The variable speed design that worked best in our testing was the dial type rather than trigger type, as the trigger control can add fatigue to the operator’s hand and can be difficult to use with bulky gloves.
Two similar saws; the DeWalt saw has trigger controlled variable speed, the Milwaukee does not
Blades
The number of teeth per inch or TPI can range from 3 to 24. This allows the blade to be designed specifically for the type of material being cut. The numbers on the blade indicate the number of TPI. Lower tooth count blades are for softer materials such as wood or plastic. Higher tooth count blades are used for harder materials such as metals. Low tooth count blades are for rough and fast cutting. High tooth count blades are for fine or slow cutting. A 5-TPI blade will not cut through hard metal. A balance must be found when selecting a blade for extrication. It must be capable of cutting all the materials you encounter.
Blade thickness is also very important. We found a big difference between blades commonly available at your home improvement store and the much higher quality blades used in rescue or industrial applications. Thicknesses are available from .020 inches to .068 inches. A thicker blade has better durability and heat dissipation.
Examples of blade types and brands that we tested
The example shown below is a demolition blade with 5-TPI. It is designed to rough-cut quickly through wood with occasional nails.
This is an example of a metal-only blade with 24-TPI. It has the small tooth size required for metal use, but will not quickly or effectively cut other materials.
Here is an example of a 10-14-TPI blade designed for metal cutting. Note the asymmetrical tooth pattern for use on a wide variety of metal thickness and hardness.
A common problem encountered when using the saw in the field is the blade falling out. The blade’s spring loaded retaining pin in the saw failed to hold on to the blade or broke off. What could have caused this?
All reciprocating saw blades are painted during manufacturing. As you can see below, on some blades, the paint will accumulate in the retaining hole and prevent secure mounting in the saw. All blades are manufactured with a standard size mounting hole for the retaining pin in the saw. Have you noticed the small tail on the mounting end of the blade? There are many ideas about what this tail is for. These range from “I don’t know” to “indexing the blade in the saw” to “manufacturing process”.
Here is an example of what that little tail is really for. It is designed as a tool by all manufacturers to clean out the extra paint from the mounting pin hole in the blade. This will allow secure engagement of the retaining pin.
Simply twist the blade to clear out the extra paint. Now the blade is ready for use. (This seemed pretty obvious once we found this out.)
Below are some examples of blades showing different tips. A pointed tip is designed to allow a plunge cut through materials such as drywall or sheet metal. The blade shown on the left would not be suitable for plunge cutting. It is designed for material that has an exposed edge such as pipe or board.
Metallurgy 101
When cutting metal, you have to consider the hardness of different materials being cut. This can vary from soft metals such as aluminum or brass, to hard metals such as tungsten or titanium. If you have ever cut aluminum with a cut-off saw, you will have seen the blade gum up with molten aluminum. Have you ever drilled into a piece of steel and watched the drill bit go up in smoke? Why did this happen? The answer is heat. In both examples, metal overheated and prevented the cutting of the material. The aluminum is softer than the cut-off saw blade. Enough heat was generated by the saw blade to melt the aluminum and cause the blade to be clogged. The steel is at the opposite end of the spectrum. It is much harder metal, so the heat generated caused the drill bit to melt away the cutting edge of the bit.
In each of these examples, preventing heat build-up will improve cutting performance. There are two ways to manage heat when cutting metal; slower speed and/or use of cooling lubricant. Industrial metal cutting machines manage heat by spraying a water-based lubricating coolant on the cutting tool. A band saw manages heat by using a slower cutting speed which enables the blade to cool as it cycles back around to cut again. The tool steel must maintain hardness in order to continue cutting the material at hand. Overheating a reciprocating saw blade causes it to lose its tempering (hardness), and the ability to cut. A reciprocating saw has a short cutting stroke (approximately 1 ½”) and is unable to cool between strokes. It will overheat quickly, the blade will lose its tempering, and the teeth will melt away. It is vital to keep the reciprocating saw blade cool.
Testing
We compared the cutting action of the same blade using different methods on a hardened steel pipe. The first cut was performed with the saw at wide open throttle (WOT) (3000rpm) without lubricant. The blade lasted only a few seconds before it overheated and lost its tempering. At this point the teeth melt away quickly, turning the blade into a butter knife. The blade below was used at WOT without lubricant. Note the temperature as measured with an infrared thermometer.
Next, we tried the same blade type at WOT while spraying it with a dish soap and water mix. The temperature of the blade itself was drastically reduced, but the teeth still overheated. The blade lasted a few seconds longer, but the teeth were still melted off in a short period of time as shown below.
We then tried the same blade type at half speed (1500 rpm) with no cooling spray. The blade completed our test cut. The slower cutting speed allowed better heat dissipation away from the cutting teeth. While the blade still reached 220 degrees and melted the paint, the heat build-up in the tooth area was not enough to damage the teeth of the blade as shown below.
Our last cut was also at half speed with the addition of soapy water to cool the blade. This test cut was completed much faster than the non- lubricated blade at half speed, with the added benefit of a blade that showed almost no wear on the teeth or sides as shown below. Note the lower temperature and tooth condition.
The alternating, offset tooth pattern depicted in the photo below is known as the “kerf” of the blade. This allows the blade to make a cut wider than the actual thickness of the blade, preventing binding.
The picture below shows the difference between the cutting ability of the same blade type, using different cutting methods.
The upper blade, used at WOT, didn’t cut very far before the teeth burned up. Slowing the saw speed down and cooling the blade allowed us to complete this cut quickly with no problems.
Findings
The reciprocating saw is a valuable tool due to its simplicity, low cost and versatility when used properly.
Saw Types and Brands
We utilized numerous types and brands of saws during our testing. Some saws are green, some are red, some are yellow, some are battery powered, some are corded, some are $100, some are $200. Regardless, they all have a blade that moves back and forth. They all work well. The key is to find what works for you.
Speed
A slower cutting speed that does not stall the saw, combined with proper shoe use to prevent “bouncing the saw”, provides a faster cut. Slowing down allows you to cut faster by controlling the heat produced. Blades last longer and are able to finish the job without replacement.
Lubricant
We found a spray bottle filled with a 10:1 water and soap mixture to be a very simple and effective tool in controlling heat. This mixture also lubricates the blade cutting teeth and blade sides to prevent binding in the cut zone. Adding a sticky soap mixture to the cutting area also cools and encapsulates the metal chip debris that could get on a patient or embedded in clothing.
Blade Selection
We tested every blade we could get our hands on and found a wide range of results. Our favorites for extrication purposes are:
Starrett (www.starrett.com)
- King Cut / Fire Rescue and Demolition - Available in 6, 8,9 and 12” lengths, .063” thickness, 10-14 TPI
M. K. Morse (www.mkmorse.com)
- Fire and rescue Blade -available in 6, 9 and 12” lengths .062” thickness, 10 or 14 TPI
These blades may cost more than the ones you pick up in bulk at the local home improvement store, but they will exceed your expectations of performance and durability. You want the best tool available to perform an extrication as fast as possible. Good blades are worth the investment.
Final Thoughts
We don’t usually do articles about tool use in the fire service., but we thought this was important enough to spend a year researching and proving our findings. The benefit of our testing became clear. Slower blade speed is the biggest factor when using a reciprocating saw. Slower is definitely faster. A little self control and 10 minutes of practice with this valuable tool can drastically increase your proficiency in cutting during an extrication, no matter what material you encounter. Remember these three things; clean the mounting hole on the blade, control your cutting speed and lubricate the blade.